Robot e cobot con sistema di visione 3D per il settore automotive (e non solo): i vantaggi nell’esperienza Pick-it
L’impiego di sistemi di visione nella produzione industriale sta crescendo notevolmente: l’ultimo report di Grand View Research stima un mercato che nel 2025 varrà più di 18 miliardi di dollari in tutto il mondo, con un tasso annuo di crescita intorno all’8%.
Del resto sono ancora molte le attività che possono essere opportunamente ottimizzate, per esempio attraverso il ripensamento delle modalità con cui vengono svolte, con la finalità di arrivare a un impiego più efficiente di tutte le risorse a disposizione:
in ambito industriale, si stima che la forza lavoro manuale che viene utilizzata per spostare delle parti da ceste e/o piani di alimentazione, dove si trovano spesso alla rinfusa, alle postazioni dove avviene la fase successiva della loro lavorazione, sia ben il 40%.
All’interno di questa statistica, ci sono alcune attività che continuano a trovare nella particolare destrezza degli operatori e nella capacità davvero unica di questi – frutto dell’esperienza – di valutare le caratteristiche delle parti e il modo migliore per gestirle, la risposta più “cost effective” disponibile: pensiamo per esempio alle situazioni in cui è necessario aprire di volta in volta delle buste di plastica, un’attività complessa e costosa da automatizzare.
Altre operazioni possono invece trovare nelle automazioni la risposta più adeguata, a vantaggio anzitutto della salute degli operatori sia dal punto di vista dello stress fisico sia sotto il profilo dello stress psicologico, analizzato anche sulla base delle più recenti teorie dell’ergonomia cognitiva:
- attività ripetitive, fatte di continuo, possono portare a situazioni di malessere fisico che si sviluppano un po’ per volta, nel tempo, e spesso sono dovute ad atteggiamenti o movimenti non corretti, che come conseguenza possono portare a problemi alle articolazioni e alla muscolatura fino a richiedere riposo e terapie
- durante il lavoro sulle linee gli addetti possono entrare in contatto, accidentale e traumatico, con macchinari e processi in corso, rischiando incidenti che talvolta hanno, purtroppo, conseguenze anche gravi
- gli operatori che svolgono sempre la stessa mansione sono più soggetti al rischio di distrazioni ed errori, specie quando l’attività è banale e dev’essere svolta in velocità
- per le operazioni più ripetitive, l’impiego dei robot assicura uno svolgimento preciso e permette di riqualificare gli addetti su altre mansioni a più alto valore aggiunto
- sotto il profilo della produzione, invece, mediante l’impiego di robot l’attività può continuare senza soste, a parte quelle necessarie per alimentare la postazione di presa (e anche qui, possono esserci margini per ulteriori ottimizzazioni grazie alle opportune automazioni).
In un passato neanche troppo lontano, automatizzare attività come l’alimentazione delle parti (pick&place, ossia presa-movimentazione-rilascio) era possibile solo attraverso delle automazioni cosiddette “spinte”: le linee produttive venivano progettate intorno al robot che dovevano ospitare; questo robot era in grado di realizzare un solo movimento, sempre identico, ad altissima velocità.; anche l’alimentazione e l’output dovevano, però, seguire degli standard predefiniti, non modificabili a meno di metter mano all’intera linea produttiva (con i tempi e i costi che questo comporta).
In seguito sono stati introdotti dei sistemi di visione 2D, che rappresentano sicuramente un’evoluzione e una semplificazione rispetto al modello precedente e hanno permesso a tante più aziende di integrare con maggiore facilità i robot nelle linee produttive.
La visione 2D consente di risolvere l’alimentazione quando si tratta di parti tutte uguali, poste ordinatamente su un piano, separate tra loro (in modo da lasciare uno spazio per la presa) e lavorabili dal robot seguendo dei percorsi precisi: in questo modo si riescono a superare le difficoltà create alla visione 2D principalmente da superfici riflettenti (delle parti) o da un’illuminazione non uniforme del piano, che può generare delle ombre.
L’evoluzione della tecnologia ha permesso di arrivare a un ulteriore livello, rappresentato dalla visione 3D che trova nel nostro partner Pick-it una delle aziende leader al mondo.
Grazie ai sistemi di visione 3D, che oggi come oggi hanno dimensioni molto contenute tanto che possono essere montati al braccio o al polso del robot, è possibile superare le criticità incontrate dalle soluzioni precedenti.
La visione 3D permette infatti di gestire delle parti anche quando:
- sono sovrapposte alla rinfusa,
- hanno forme differenti tra loro
- lucide, riflettenti o anche trasparenti
Un esempio di questa versatilità l’abbiamo già visto parlando di un’applicazione robotica che ha permesso di lavorare sul bin picking di oggetti complessi per i sistemi automatizzati, come le siringhe.
Ma la visione 3D realizzata con Pick-it trova impiego in tantissime applicazioni industriali.
Un ambito particolarmente attento a questa evoluzione è il settore automotive, dove un sondaggio svolto dai nostri partner ha evidenziato che quasi 1 fornitore su 2 (selezionato tra i top 100 al mondo) ha già integrato, oppure valuta di integrare entro al massimo un paio d’anni, un sistema di visione 3D sui robot impiegati nella produzione.
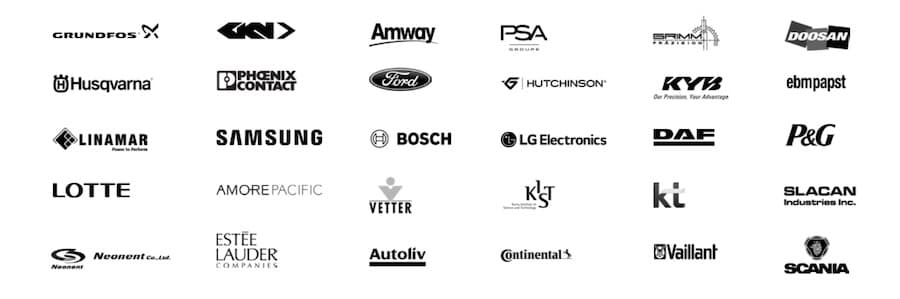
elenco di aziende del settore automotive che già hanno scelto e impiegano il sistema di visione Pick-it 3D (fonte: Pick-it)
Alcuni materiali si prestano particolarmente per essere lavorati con sistemi di visione 3D: sono quelli con una forma semplice, simmetrica oppure asimmetrica con differenze molto pronunciate da un estremo all’altro del pezzo, dimensioni superiori a 20 mm e una superficie che può anche essere trasparente o riflettente (cilindri in metallo, ammortizzatori, bulloni, ruote, cilindri motore, barre stabilizzatrici, manicotti, bielle, connettori, ingranaggi, albero a camme, elementi di fissaggio).
In questo video, KYB Americas Corporation racconta la sua esperienza che ha portato a ottenere un miglioramento dell’alimentazione delle parti nella misura del 50% rispetto alle diverse modalità sperimentate in precedenza
Ma a fronte di un’adeguata configurazione, i sistemi di visione 3D Pick-it sono in grado di lavorare anche altre parti, con forme diverse e dimensioni fino a un minimo di 5 mm: alberi di trasmissione, alberi a gomiti, bielle, coperchi di distribuzione, blocchi motore, volante, frizione, boccole in gomma, termostati…
Adam Wiltsie, direttore di stabilimento in Vanamatic (un’azienda statunitense attiva sia nell’industria automotive che a supporto del settore aerospaziale), racconta di aver imparato a configurare un robot in autonomia pur senza aver avuto una preparazione specifica, grazie alla semplicità d’uso delle varie parti che compongono la cella collaborativa, ad alcuni momenti di formazione e ai diversi tutorial disponibili in rete, spesso realizzati anche dai nostri partner (Pick-it, ma anche Universal Robots, Robotiq e altri).
Attraverso l’impiego dei cobot equipaggiati con sistemi di visione Pick-it l’azienda è riuscita a rendere delle attività che prima erano svolte al 100% da persone operazioni automatizzate in larga parte (circa l’80%) superando il problema di un turnover che arrivava a coinvolgere anche 30 diversi addetti in un anno per quella specifica mansione.
Sempre negli Stati Uniti, in Michigan, 21st Century Plastics Corp. ha impiegato i robot nella transizione dall’indotto dell’industria automobilistica, per cui lavorava esclusivamente, allo sviluppo di un nuovo modello di business nella costruzione di seggiolini per stadi, palazzetti, teatri e altri luoghi per le grandi manifestazioni:
questa scelta ha permesso all’azienda di superare i tempi morti nella produzione, realizzando cicli automatizzati da 45 minuti che gli addetti possono far svolgere in autonomia al robot mentre si occupano di altre mansioni, e di fare fronte alla carenza di manodopera dovuta alla piena occupazione raggiunta in quelle aree.
Impiegando i robot collaborativi con i sistemi di visione per 24 ore al giorno, 5 giorni alla settimana, la stima realizzata da 21st Century Plastics Corp. per il tempo di ROI è di soli 5 mesi.
Anche GKN, azienda leader nella realizzazione di componenti destinate alle industrie del settore automobilistico e aerospaziale, ha impiegato i sistemi di visione dei nostri partner per automatizzare diverse attività.
In particolare, in uno dei suoi stabilimenti GKN ha affidato la presa di parti dai contenitori a 30 robot Fanuc abilitati con Pick-it 3D.
Attraverso questa dotazione, GKN è riuscita ad automatizzare la maggior parte delle attività necessarie per la produzione del cambio delle automobili, un processo che coinvolge fino a 50 macchine differenti.
Il trasferimento di ciascuna parte da lavorare tra le diverse celle robotiche viene svolto dai cobot con sistema di visione perché questi sono in grado di realizzare la presa anche dei componenti che cadono all’interno delle scatole o cambiano posizione, che in genere sono il 10% del totale, senza fermi o rallentamenti della produzione.
Tante esperienze diverse, legate a vario titolo al settore automotive, e tutte accomunate dal sostanziale aumento della precisione, della velocità di realizzazione e della produttività delle soluzioni integrate nelle linee grazie all’impiego dei sistemi di visione 3d Pick-it.
Per conoscere più da vicino il prodotto, scoprire tutte le numerose potenzialità d’impiego e sottoporci la tua idea di applicazione robotica collaborativa da sviluppare anche con un sistema di visione, contattaci attraverso la scheda dedicata del sito: i nostri commerciali sono a disposizione per un confronto preliminare senza impegno e per valutare insieme la soluzione più efficiente per il tuo business.